20.10
Dynamic running record report and meter reading system
Reports are automatically
generated according to the analysis policy files(.pda) in \BigData, the
default record time interval is one second. Counting accumulative values(I=1 in Config.csv) by minute or the
average value(I=2) of the accumulative value or instantaneous
value(I<>1 or 2), a value is calculated per hour. Only instantaneous
value is calculated for bool and string.
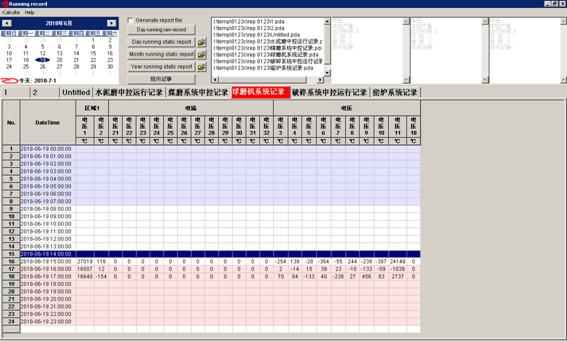
Figure 20.18 Dynamic operation record and meter
reading system operation interface
20.11 A
hot rolling mill main drive SL150
SL150 is Siemens' new
generation high-power alternating current frequency main drive system, with
core units of Simotion D445 (or D455) template and Sinamics CU320 template.
The PDA system collects data through standard Ethernet and Profinet, with a
data refresh cycle of 1ms.
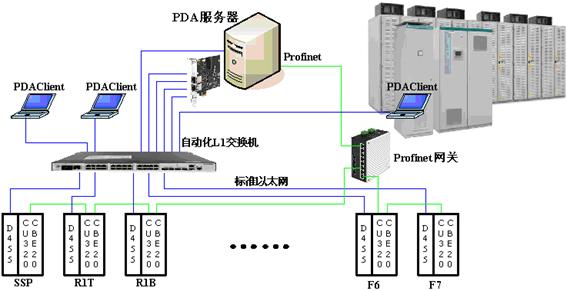
Figure 20.19
Main Drive Data Collection Network Diagram
20.12
Reforming of Data Acquisition System
Some special equipment,
special communication network and special servers are used in some data
acquisition systems. The system is very complex and expensive. Once it breaks
down, it is very difficult to recover. The following figure is a
transformative replacement of PDA system used in a steel plant.
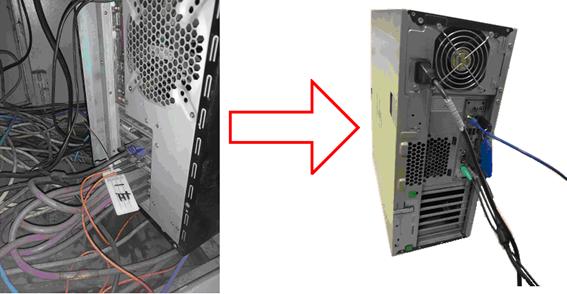
Figure 20.20 PDA System Transformation Host
Network Diagram
20.13
Statistical Process Control
The purpose of SPC is to
prevent, control and forestall.
The main functions of SPC are:
real-time monitoring and early warning of the production process, timely
taking measures for abnormal fluctuations, real-time improvement; judging
whether the process fluctuations are random or abnormal fluctuations;
realizing process stability and control.
SPC index is calculated for
the data between x1 and x2 of the first curve in the current display area.
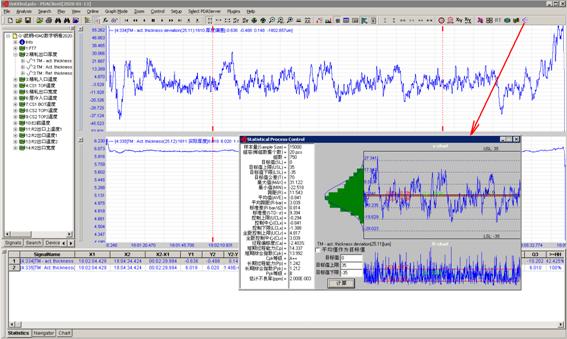
Figure 20.21 Statistical Process Control SPC
Curve
20.14
Data Acquisition and Point Map Analysis System of a Brewery
Collect data from over 30 PLCs
and electricity meters. The point maps include CO2 recovery and consumption,
low-voltage electricity meters, high-voltage electricity meters, water
volume, compressed air, steam, etc. Second-level data is promoted to SQL
Server, millisecond level data is promoted to InfluxDB, and all tables are
automatically created, with a structure consistent with the PDA system.
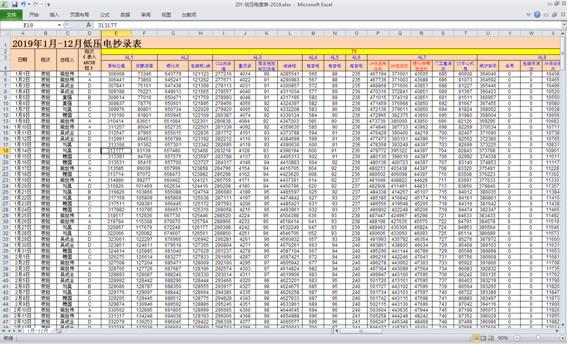
Figure 20.22 Energy consumption data collection
for breweries
20.15
CO2 Recovery Prediction and Measurement Data Analysis System for a Beer Factory
Based on the mother liquor and
fermentation tank data, the CO2 recovery curve can be predicted and compared
with the real-time curve for analysis, achieving balanced and stable
production of CO2 and beer.
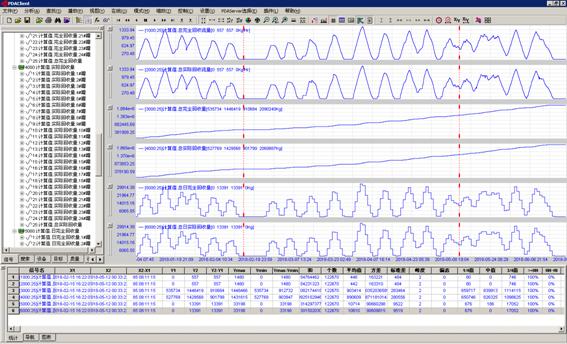
Figure 20.23 CO2 Recovery Prediction Curve
20.16
Unmanned locomotive and intelligent hot metal transportation system
Including driverless,
uncoupling, parking anti slip, positioning, derailment detection,
environmental awareness, equipment support, traffic scheduling, remote
centralized control and other subsystems, any failure may cause catastrophic
consequences.
The follow is locomotive
operation.
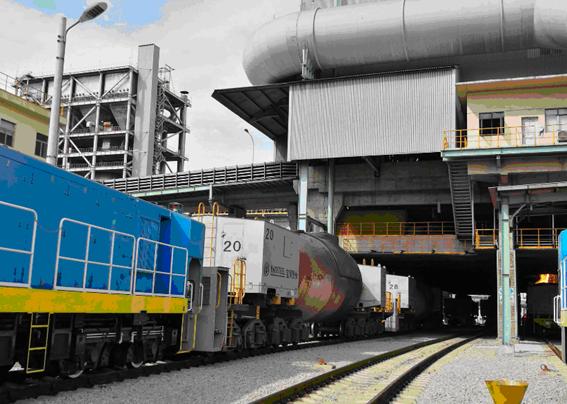
Figure 20.24 Diagram of Molten Iron Transport
Locomotive
The follow is locomotive
operation status.
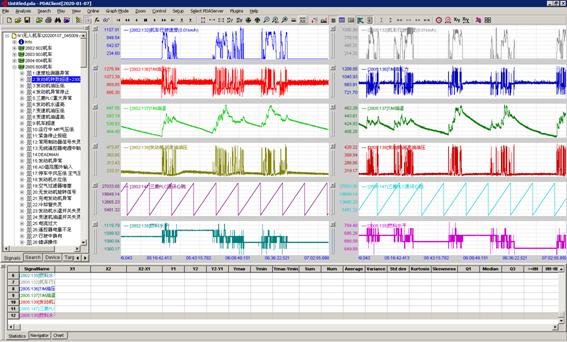
Figure 20.25 Data curve recorded by unmanned
locomotives
20.17
All-weather unmanned wharf
It includes unmanned port
machinery, steel coil automatic lifting, intelligent management and control
of the terminal and other subsystems, which liberates the operators from the
heavy and dangerous environment.
The follow is automatic
lifting of steel coil at wharf.
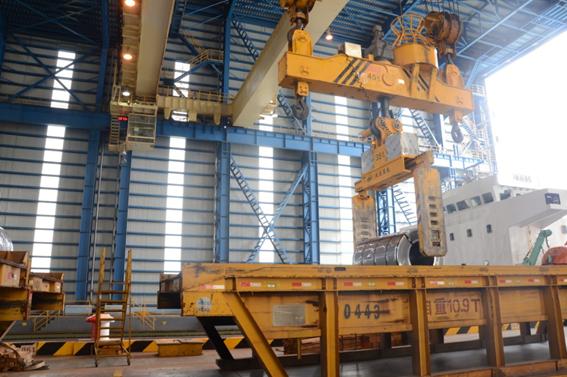
Figure 20.26 All weather dock operation site
The follow is wireless signal
strength and SNR of leaky wave cable.
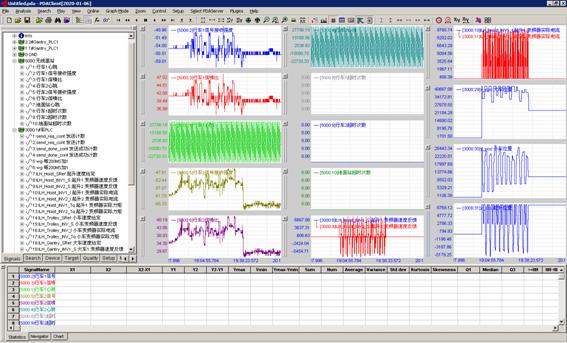
Figure 20.27 All weather dock PDA monitoring
curve
20.18
Electro hydraulic servo control system
The servo motor drives the
hydraulic cylinder for high-precision closed-loop control, Its positioning
accuracy can reach um level, Servo valve and large-scale hydraulic station
are cancelled, so the system has low cost, small maintenance and high
reliability.
The follow is MS level data
curve.
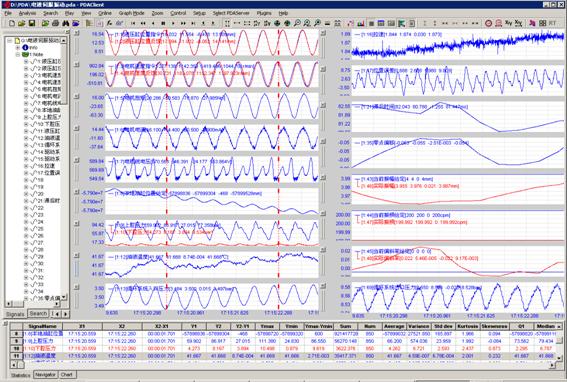
Figure 20.28 Millisecond level data curve of the
electro-hydraulic servo control system
The follow is day data of
second level.
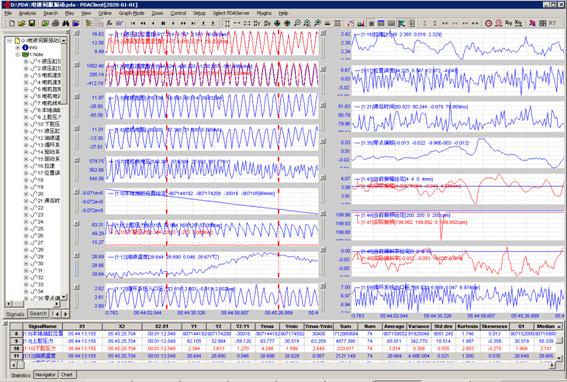
Figure 20.29 Second-level Data Curve of Electro-hydraulic
Servo Control System
20.19
Automobile monitoring system
The car is controlled by CAN
bus. PDA supports standard frame and extended frame. It can collect all frame
IDs at high speed. It is an effective tool for car monitoring, development
and driverless debugging.
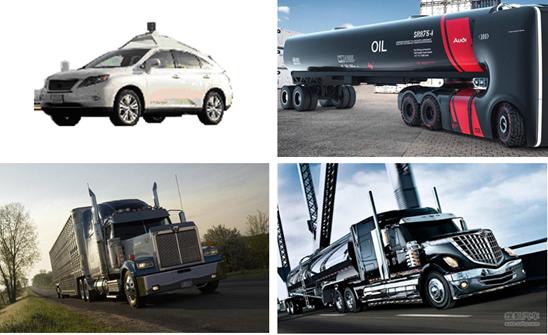
Figure 20.30 Various Cars Based on CAN Bus
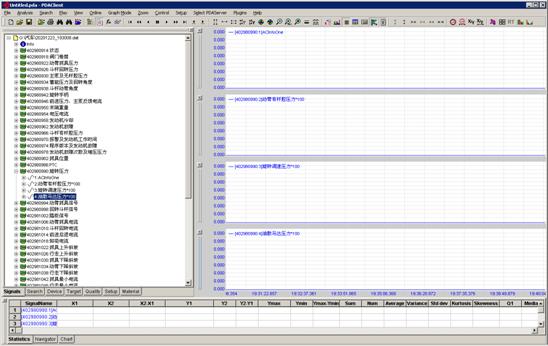
Figure 20.31 CAN Bus Data Collection for a Certain
Car
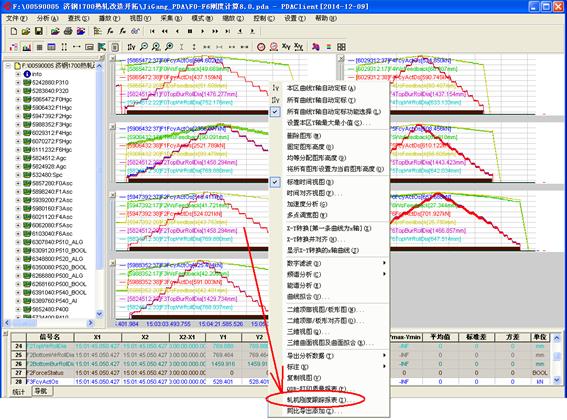
Figure 20.32
Measurement curve of rolling mill stiffness
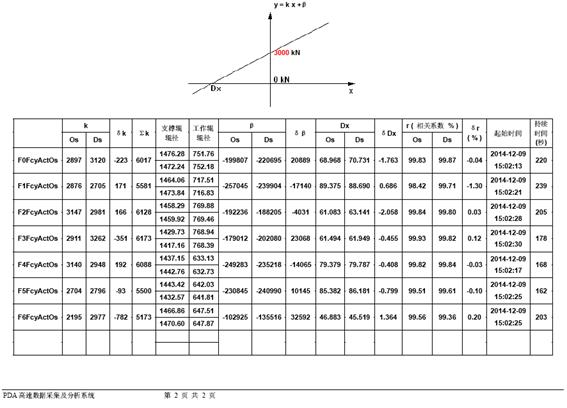
Figure 20.33
Linear fitting results of rolling mill stiffness
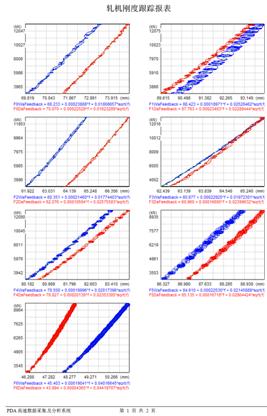 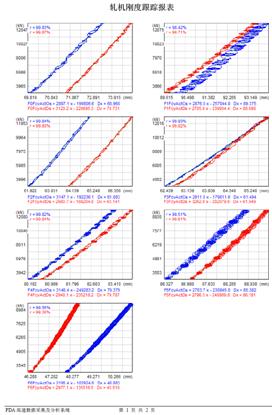
Figure 20.34
Original and fitted curves of rolling mill stiffness
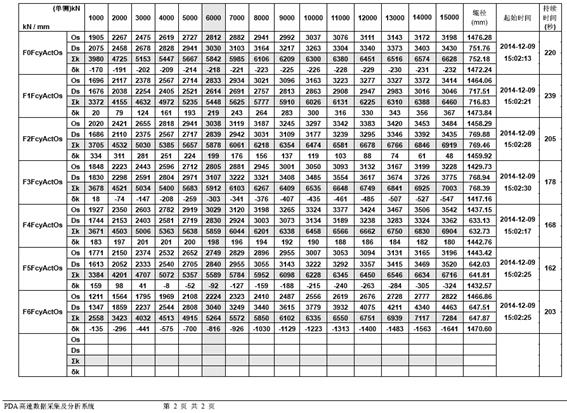
Figure 20.35
Calculated stiffness under various rolling forces
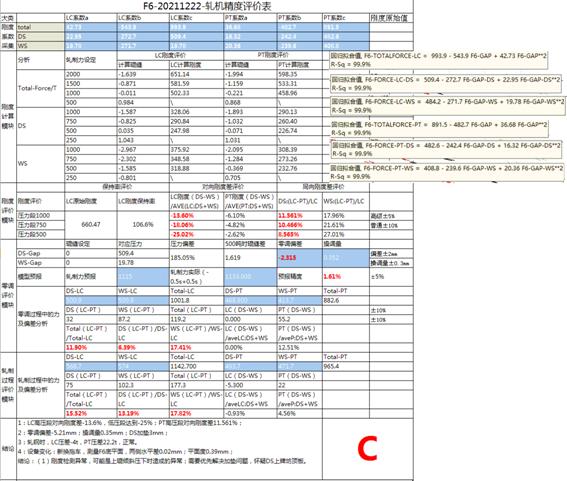
Figure 20.36
Stiffness Evaluation of a Steel Plant
20.21 MPT
- Mill Pacing Tracing
MPT (Mill Pacing Tracing) calculates the accurate tracking
position of the head and tail once every 50ms.
Reduce waiting for steel placement.
The rolling pacing is increased by 3 seconds, and an additional 20
pieces of steel can be produced per day.
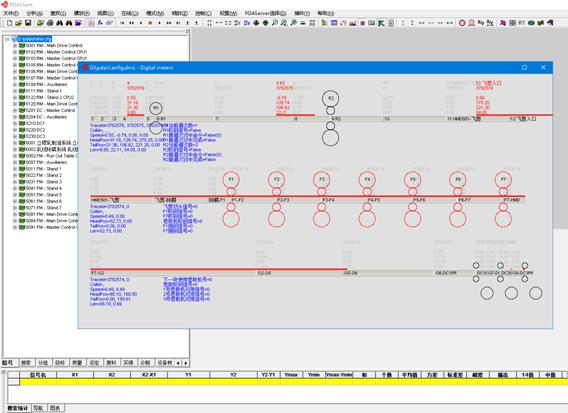
Figure 20.37
Rolling Pacing Tracing
20.22
IGBT
Flexible DC Chopper Power Supply - Green Intelligent Super Arc Furnace
The project won the second
prize of the National Science and Technology Progress Award. The PDA system
can collect 20KHz data of current and voltage in each phase, and perform
online and offline analysis of harmonics such as 3, 5, 7... 13, 15, 17.
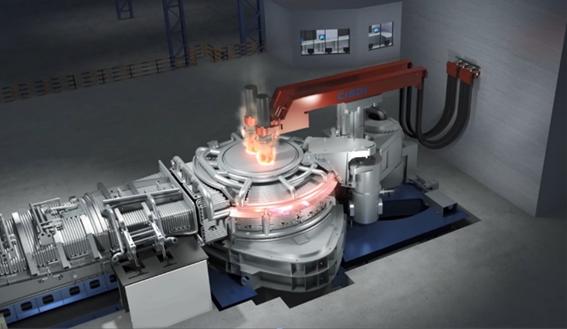
Figure 20.38 Green Intelligent Super Arc Furnace
The application of advanced
technologies such as new IGBT flexible DC power supply technology, electrode
stepless dual control intelligent regulation technology, continuous
preheating technology for scrap steel, step wise continuous feeding
technology for scrap steel, air-cooled contact needle bottom electrode
technology, dioxin treatment and waste heat recovery technology, intelligent
steelmaking technology, etc. can quickly respond to the smelting energy supply
demand in the electric arc furnace and respond to short circuit and over current
impact conditions, shorten the smelting cycle to within 30 minutes, and
reduce power consumption to 250-300 kWh/t, The electrode consumption is 0.6-0.8kg/t, which is a new generation of
green, energy-saving, environmentally friendly, and efficient electric
furnace. Compared with conventional electric furnaces, it has great
advantages in improving production efficiency, reducing electricity and
electrode consumption, and improving metal recovery rate.
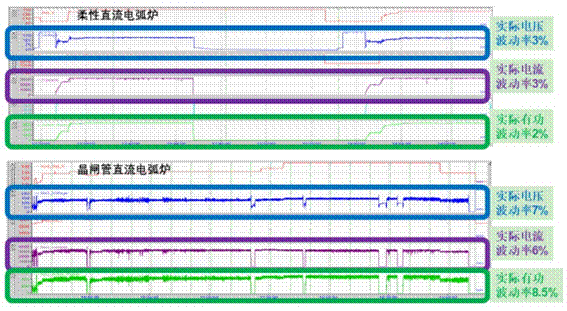
Figure 20.39 Performance Comparison Curve
between Green Intelligent Super Electric Arc Furnace and Traditional Electric
Arc Furnace
20.23
Mobile APP
PDA.apk is an Android
installation package that requires storage permissions. The on-site
configuration information for each project needs to be downloaded to a
storage card for future use.
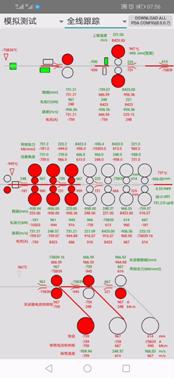
Figure 20.40 Real time data display and
production monitoring system for various styles
20.24
PLC ring network fault detection
The ring network composed of
multiple S7-1500 controllers and HMIs seems to be working properly. When the
PDA was connected to the network for 2ms data collection, it was found that
dozens of data packets were lost every 6 seconds. However, when the PDA was
directly connected to the PLC, everything was normal. Further investigation
revealed that disconnecting the ring network was also normal. Later, the PLC
version was lowered and the ring network was normal. It's not that the higher
the PLC version, the better.
20.25
Mathematical Model Log
Modern steel rolling
mathematical models are becoming increasingly complex. The traditional method
is to write key data into. log files and analyze the. log text files when
problems are found, which is not intuitive and inefficient. By sharing memory
or networks, a large amount of model data can be recorded in PDA systems,
accelerating the debugging progress of the model and the convenience and
accuracy of fault analysis.
|